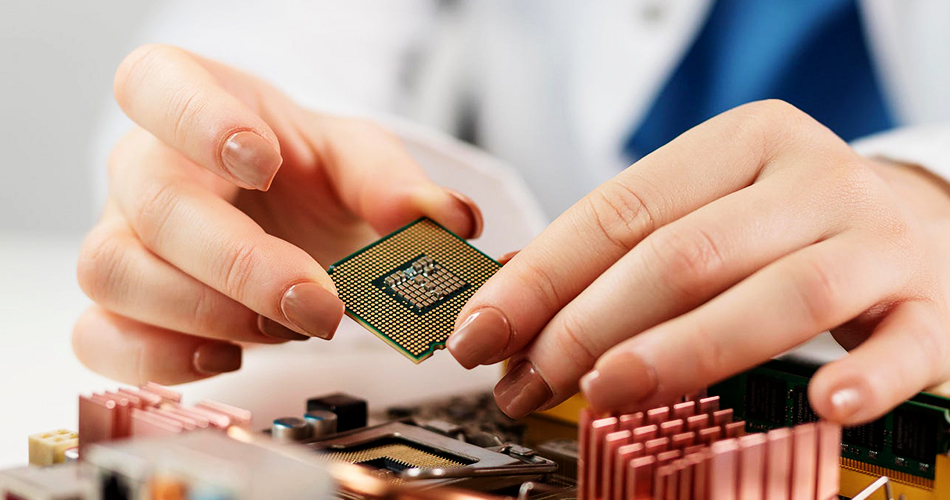
在PCBA加工(Printed Circuit Board Assembly,印刷电路板组装)过程中,质量控制始终是确保产品性能与可靠性的关键环节。然而,由于PCBA加工工艺的复杂性和涉及的变量众多,质量控制面临诸多挑战。如果这些挑战得不到有效应对,将直接影响产品的最终质量,甚至导致客户投诉和市场份额的流失。本文将探讨在PCBA加工中常见的质量控制难题,并提供应对这些难题的有效策略。
1. 原材料质量控制难题
挑战分析:
PCBA加工中的质量控制首要挑战在于原材料的质量。一旦使用了质量不合格的元器件或PCB板材,将严重影响整个产品的质量。元器件的假冒伪劣、规格不符或存储不当,都会导致后续工艺中的不良品率增加。
应对策略:
为了解决原材料质量控制的难题,企业应建立严格的供应商管理体系,选择经过认证的优质供应商,并定期进行质量审计。此外,在材料入库时,企业应进行严格的来料检验,确保所有元器件和材料的规格和性能符合要求。对于关键元器件,还可以采用批次追溯和严格的库存管理,以保证其在最佳状态下使用。
2. 焊接工艺中的质量控制难题
挑战分析:
焊接工艺是PCBA加工中的核心环节,涉及到将元器件固定到PCB上的过程。由于电子产品日益小型化和复杂化,焊点的数量和密度都在增加,稍有不慎就可能出现虚焊、冷焊、焊点开裂等问题,这些问题都可能导致产品性能下降或失效。
应对策略:
解决焊接工艺中的质量控制难题,需要从多个方面入手。首先,应选用适合的焊接设备和焊接工艺,如回流焊、波峰焊或选择性焊接等。其次,严格控制焊接温度曲线,确保焊接过程中的温度和时间参数精准可控。此外,企业应定期维护焊接设备,并进行焊接工艺的优化调整,以适应不同产品的需求。
3. 组装过程中的质量控制难题
挑战分析:
在PCBA加工的组装阶段,元器件的正确放置和固定至关重要。由于手工操作和自动化设备的复杂性,错装、漏装、偏移等问题时有发生,这些问题不仅影响到产品外观,更可能导致电路功能的失效。
应对策略:
在组装过程中,应充分利用自动化设备如自动光学检测(AOI)和自动X射线检测(AXI)系统,对每一道工序进行在线检测。这些检测系统可以实时识别和纠正装配中的问题,确保每个元器件都准确无误地安装在指定位置。此外,企业还应加强操作人员的培训,提升他们的工艺操作水平,减少人为失误。
4. 测试和验证环节的质量控制难题
挑战分析:
PCBA加工的最后一个环节是产品的测试和验证,这是确保产品功能正常的重要步骤。然而,由于测试设备的局限性或测试方法的不完善,可能出现漏检、误检的问题,导致不良品流入市场。
应对策略:
为提升测试和验证的准确性,企业应引入先进的测试设备和测试方法,如功能测试(FCT)、在线测试(ICT)和环境应力筛选(ESS)等。此外,企业还可以通过构建产品的数字孪生模型,模拟实际使用环境中的性能表现,从而更全面地验证产品的质量和可靠性。
结语
PCBA加工中的质量控制难题多种多样,企业只有通过系统化的应对策略才能有效解决这些挑战。通过加强原材料质量管理、优化焊接工艺、精细化组装操作以及全面的测试验证,企业可以大幅提升PCBA加工产品的质量水平,减少不良品率,并增强市场竞争力。在质量控制得到有效保障的前提下,PCBA加工企业将能够持续为客户提供高质量的产品,赢得市场和客户的信任。