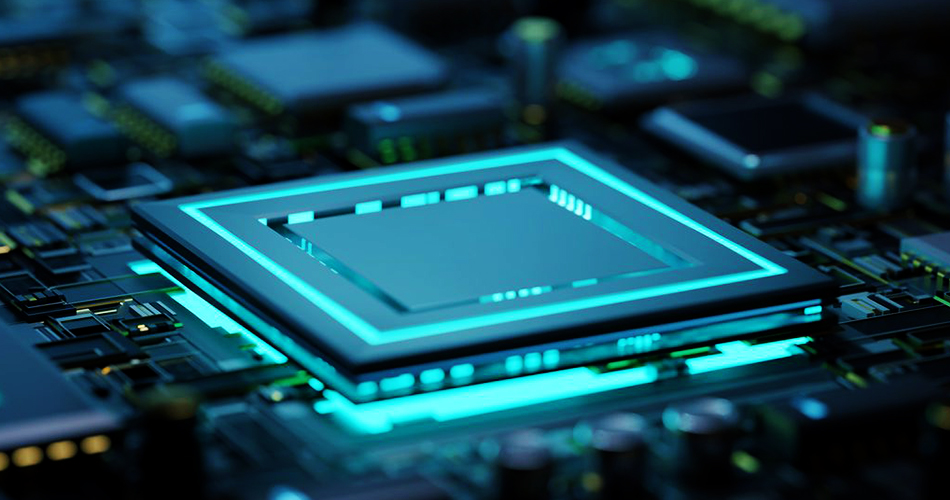
在PCBA(Printed Circuit Board Assembly,印刷电路板组装)加工中,工序布局的优化直接影响生产效率、成本控制和产品质量。一个合理的工序布局可以减少生产过程中的时间浪费和物料搬运,提高生产线的整体效率。本文将探讨如何优化PCBA加工中的工序布局,以实现更高效、更经济的生产流程。
1、评估现有工序布局
问题: 当前工序布局可能存在不合理之处,如物料流动不畅、操作人员频繁移动等,影响生产效率。
对策:
·进行流程分析: 对现有工序布局进行详细分析,绘制生产流程图,识别生产过程中的瓶颈和浪费点。
·数据收集: 收集生产数据,包括生产时间、物料流动、设备利用率等,了解现有布局的实际运行情况。
·反馈收集: 向生产线员工和管理人员收集反馈,了解他们在操作过程中遇到的问题和改进建议。
2、设计合理的工序布局
问题: 不合理的工序布局可能导致物料搬运距离过长、操作流程复杂,从而降低生产效率。
对策:
·流程优化: 根据流程分析结果,优化工序安排,尽量减少物料在生产线上的搬运距离和时间。将相关工序布置在接近的位置,形成流畅的生产线。
·单件流布局: 采用单件流布局,将每个工序按照顺序布置,使每个工序完成后立即传递到下一个工序,减少等待和积压时间。
·模块化设计: 将生产线设计成多个功能模块,每个模块负责特定的工序。这种布局能够提高生产灵活性和维护效率,方便进行调整和扩展。
3、引入自动化设备
问题: 手动操作和传统设备可能限制生产线的效率和精度。
对策:
·自动化解决方案: 引入自动化设备,如自动上下料机、输送带和机器人,以提高工序的自动化水平,减少人工操作和错误。
·智能控制系统: 使用智能控制系统对生产线进行实时监控和调整,优化设备的运行状态和生产流程,提高生产效率和产品一致性。
·数据集成: 将自动化设备与生产数据系统集成,实现数据的实时采集和分析,优化生产过程和设备利用率。
4、实施持续改进
问题: 工序布局的优化不是一次性的过程,需要不断调整和改进以适应生产需求的变化。
对策:
·定期评估: 定期对工序布局进行评估,分析生产数据和员工反馈,识别需要改进的地方,进行布局优化。
·实施改进: 根据评估结果实施改进措施,如调整设备位置、增加工作站或改进物料搬运方式,持续优化工序布局。
·培训与管理: 对员工进行工序布局优化的培训,确保他们理解新的布局安排,并遵守操作规范,以提高生产线的整体效率。
5、考虑安全与舒适性
问题: 工序布局不合理可能影响操作人员的安全和舒适性,从而影响生产效率和员工满意度。
对策:
·安全设计: 在工序布局中考虑操作人员的安全,设置安全通道、紧急停机装置和防护措施,减少安全隐患。
·工作环境: 改善工作环境,如良好的照明、通风和舒适的工作站,提升操作人员的工作舒适性,增强他们的工作积极性和效率。
· 人体工程学: 采用符合人体工程学的设计原则,确保工作站的高度、布局和设备位置适合操作人员的工作需求,减少疲劳和操作错误。
结论
优化PCBA加工中的工序布局对于提升生产效率和产品质量至关重要。通过评估现有布局、设计合理的工序安排、引入自动化设备、实施持续改进以及考虑安全与舒适性,企业可以实现生产流程的优化,减少浪费和瓶颈,提高生产线的整体效率。一个科学合理的工序布局不仅能够提高生产效率,还能增强企业的竞争力和市场响应能力。